Восприятие того или иного материала как дорогого и правильного во многом зависит от психологии. Тут есть два момента. Во-первых, интереснее выглядит то, что ново или кажется новым. На самом деле, то, что встречается редко, — это если вкратце. Более развернуто: сейчас, во времена небывалого развития химической промышленности и тотального засилья синтетики, интерес сам собой смещается на естественные материалы. Дерево, металл, натуральные ткани или хотя бы их искусная имитация нам дороже, чем все, что похоже на пластик.
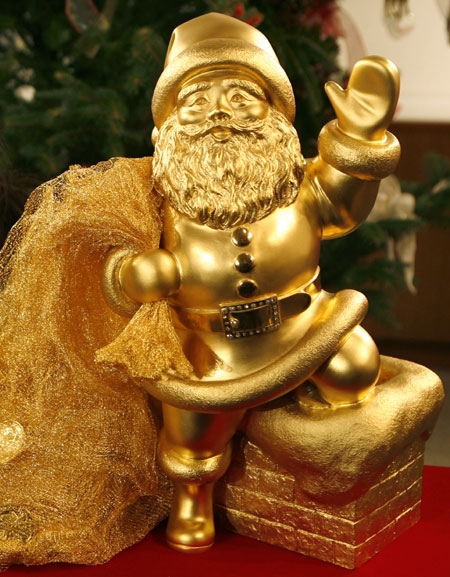
Никаких действительно дорогих материалов в ноутбуках не используют. И слава Санте!
Не стоит думать, что так было всегда. Наши бабушки и дедушки в свое время куда больше ценили как раз синтетику. Новые материалы были непривычны и выглядели по тем временам совершеннейшим космосом. И совершенно справедливо ассоциировались с прогрессом (это ведь и был самый что ни на есть прогресс). Поэтому людям они нравились, покупатели предпочитали синтетику исконно-посконным дереву, металлу и чистой шерсти с домотканым льном.
Бытовые приборы Braun в конце 50-х стали эталоном успешного дизайна. Перенеситесь мысленно в то время и представьте, насколько неземными выглядели эти устройства. Во многом это заслуга пластика
Классический для того времени дизайн телевизора Philco. Что интересно, компания Philco также пробовала свои силы в создании футуристичного дизайна — но нам он знаком лишь по игре Fallout, как один из ярких примеров ретрофутуризма
Сейчас маятник пребывает в противоположной позиции. Пластик кажется нам чем-то сугубо утилитарным и надоевшим, никакой новизны в нем давно уже нет. Куда ни глянь — всюду он. Скучно, хочется чего-то другого. Потому мы так любим металл, который наших дедушек и бабушек совершенно не возбуждал. Ну золотишко-то они любили, конечно, — но не чугуний с люминем же.
SovietSpoon Pro Unibody, классическая модель. Некоторым счастливчикам и сейчас выдается возможность пользоваться этой нетленкой
Второй момент, который вкратце можно описать как «слышал звон, да не знаю, где он». В потребительских продуктах производители уже давно и прочно переключились на синтетику. А вот в профессиональном оборудовании они все равно частенько используют металл. Не абы какой металл — но кто ж тут будет разбираться.
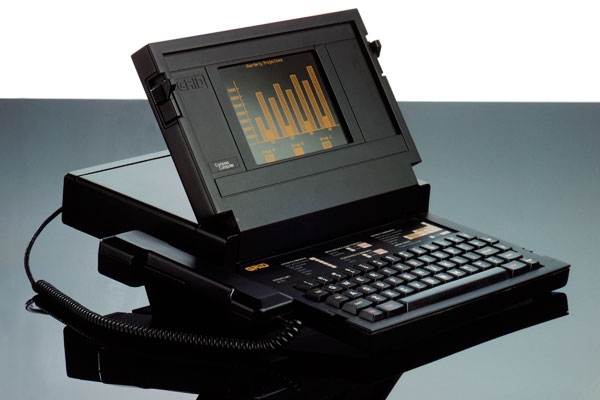
Один из первых ноутбуков, GRiD Compass: разработан в 1979 году, корпус выполнен из магниевого сплава, масса составляет 5 килограмм — по тем временам фантастически легкий. В начале 80-х этот ноутбук летал в космос, а чего добился твой макбук?
Из этого противостояния пар признаков «дешевые, пластиковые» и «дорогие, металлические» и родилось отчасти обоснованное бытовое восприятие материалов в данной области народного хозяйства. То же самое произошло и в некоторых смежных областях.
В какой-то момент производители это осознали, и на новом витке мелкотравчатого прогресса начали вовсю использовать новые предубеждения покупателей, выставляя металл напоказ даже в тех случаях, когда в конструкции его на самом деле нет. Впрочем, не будем забегать вперед и расскажем обо всем по порядку — самое время закончить с исторической справкой и перейти непосредственно к занимательному материаловедению.
Dell XPS 13 — самый богатый ассортимент материалов в отдельно взятом ноутбуке
Базовым материалом для большинства современных ноутбуков служит смесь двух синтетических материалов: акрилонитрилбутадиенстирола и поликарбоната. Сокращенно: ABS+PC или АБС/ПК, можно в обратном порядке. Первый из компонентов, АБС-пластик, примерно вдвое дешевле поликарбоната, но в чистом виде у него есть некоторые недостатки, для исправления которых в смесь и добавляют второй компонент.
Смесь ABS+PC поставляется в виде таких невзрачных гранул
На большинстве пластиковых предметов имеется маркировка, указывающая разновидность синтетики, из которой они изготовлены. Разумеется, сделано это не для удобства занимательных материаловедов, а совсем для других целей. На вид крайне сложно отличить один сорт синтетики от другого, а сортировка крайне важна в процессе утилизации и переработки отслуживших свое промышленных изделий.
Для примера разберем маркировку, которая встречается наиболее часто:
>PC+ABS FR(40)<
Она означает, что перед нами смесь АБС-пластика и поликарбоната, в которую входят антипирены — добавки, препятствующие воспламенению (FR — Flame Retardant). Для закрепления пройденного рассмотрим еще одну маркировку:
>PC GF(20)<
Это стеклопластик — поликарбонат, армированный 20% стекловолокна. Редкий, кстати, случай — встречается в ультратонких ноутбуках Samsung Series 5.
Основное преимущество этой смеси — удобство в производстве. Пластик прекрасно годится для точного литья: из него легко сделать деталь буквально любой формы, со всеми мыслимыми нюансами вроде решеток воздуховодов, ножек и подставок для крепления электронных компонентов, отверстий для винтов и миниатюрных защелок для скрепления панелей друг с другом.
Кроме того, деталь прямо «из печки» готова к поступлению на прилавок — дополнительная обработка не обязательна. Собственно, наиболее доступные ноутбуки и делают из простого некрашеного пластика. А уж что касается днища, то в 90% ноутбуков это чистый ABS+PC, без какой-либо дополнительной обработки.
В подавляющем большинстве обычных ноутбуков днище изготовлено из некрашеного ABS+PC
Впрочем, для большей внешней привлекательности с поверхностью можно что-нибудь сделать. Например, украсить ее рельефом. Или покрасить в более нарядный цвет. Или применить бархатистое покрытие soft touch. Или заламинировать — а под слоем прозрачного глянца можно нанести затейливый рисунок, который просто так стерся бы, а под ламинатом может прожить сколь угодно долго. В общем, дизайнерам работать с этим материалом максимально удобно, полет фантазии ничто не ограничивает.
Windows-планшет Samsung 700T1A : пластиковый корпус весьма убедительно имитирует металл
Что касается механических свойств, то эта смесь вполне хороша, если к характеристикам устройства не предъявляются повышенные требования. Однако следует признать: по сравнению с более продвинутыми материалами ABS+PC обладает слабым соотношением плотности и жесткости. Говоря проще: деталь из ABS+PC при равной жесткости будет значительно толще и тяжелее, чем деталь из более серьезного материала.
Чтобы без лишних затрат сделать пластик более эстетичным, можно украсить его рельефным узором. На фото — ASUS K53Ta
Это не особенно критично, например, при создании крупного ноутбука с диагональю экрана 15 дюймов. Можно сделать детали потолще, а в особо чувствительных местах добавить вставки из дешевого металла — и пусть масса устройства станет порядка 3 кило, какая разница, если ноутбук будет покидать стол только для того, чтобы переехать на соседний?
Acer Aspire V3 — глянцевый пластик плюс пластик, выкрашенный серебрянкой
Другое дело, что при нынешних ценах на нефть, невысокой марже в пересчете на одно устройство и огромных тиражах производители стараются экономить на всем, в том числе и на количестве материала. Так что даже настольные ноутбуки год от года становятся все легче — в немалой степени именно за счет более тонких (и более гибких) корпусных деталей.
Однако при создании по-настоящему мобильных ноутбуков применение ABS+PC недопустимо — при использовании этой смеси ноутбук априори получится тяжелым. Поэтому конструкторам приходится прибегать к более интересным материалам. В принципе, можно обойтись тем же пластиком, но усиленным. А чтобы усилить стандартную смесь ABS+PC, производители прибегают к армированию различными волокнами. Наиболее распространены два варианта:
1. Стеклопластик: тот же пластик, но с добавкой стекловолокна (в обозначении появляются буквы GF — Glass Fiber).
2. Углепластик: то же самое, но с углеволокном (CF — Carbon Fiber). Это еще не совсем тот «карбон», который в Need for Speed — до него тоже доберемся, но чуть позже.
Также в ассортименте химических компаний можно встретить пластики, армированные сталью (SF — Steel Fiber) и арамидом (он же кевлар), но в электронике они не прижились.
В ультрабуке Lenovo IdeaPad U410 верхняя половинка корпуса выполнена из углепластика (PC+ABS-CF(20)). Правда, не помогло: не рассчитали с толщиной детали, так что жесткости ей все равно недостает
Добавки эти очень вкусны и полезны. Скажем, 30%-е усиление стекловолокном все той же смеси ABS+PC увеличивает плотность исходного пластика примерно на 20%, но взамен удваивает прочность и жесткость. Углеволокно еще более эффективно: плотность оно повышает совсем незначительно, а по эффекту превосходит стекловолокно. Печаль одна: по стоимости армированный пластик, само собой, превосходит обычный.
Другой ультрабук того же производителя, ThinkPad X1 Carbon — углепластик использован в крышке, и она практически железобетонная
Пара производителей в недавнем прошлом также проводила эксперименты с полиамидом, усиленным стекловолокном (PA+GF). Сложно сказать, чем эти попытки закончились с экономической точки зрения, но материал оказался достаточно интересным: он обладает значительно большей жесткостью, чем любая из виденных автором армированных версий смеси ABS+PC. Правда, выглядит полиамид несколько более грубо. Так что для тех деталей, которые находятся на виду, — рабочей панели и крышки ноутбука — он подходит не лучшим образом. А вот днище из него можно сделать вполне шикарное, не хуже магниевого — только без свойственных металлу дополнительных сложностей с обработкой.
В «протоультрабуке» ASUS U36SD днище сделано из PA+GF
Что касается того углеволокна, которое «карбон как у стритрейсеров». Это тоже композиционный материал, представляющий собой несколько слоев однонаправленного или плетеного (тканого) углеволокна, пропитанных эпоксидной смолой (CF+EP). Материал этот крайне сложен в обработке. Производство даже крупных деталей сравнительно простой формы (например, корпусные панели автомобилей и мотоциклов) получается чудовищно трудоемким и дорогим. А уж для формирования всех необходимых нюансов, образующих корпус типичного ноутбука, этот материал и вовсе не пригоден.
В невесомом Sony VAIO Z13 днище выполнено из углеволокна. Так это выглядит снаружи
А так — изнутри. Лист CF+EP встроен в рамку из полиамида, армированного стекловолокном
Поэтому в тех редких случаях, когда к нему все же прибегают, «карбон» используют для формирования крупных плоских участков — скажем, для крышки или днища ноутбука он хорошо подходит. А для того, чтобы сделать все необходимые элементы крепежа, сформировать борта корпуса и прочие мелкие детали, по краям листа углеволокна приходится добавлять рамку из пластика, пригодного для точного литья. Получается достаточно сложно и дорого. Но деталь выходит очень жесткой и практически невесомой.
В Dell XPS 13 днище устроено точно так же, как в Sony VAIO Z13. С той лишь разницей, что изнутри оно омедненное, а снаружи покрыто soft touch вместо маркого лака
Следует определиться с терминологией. Вообще, у материалов и изготовленных из них предметов есть уйма всяких интересных свойств — не зря про это создали целый Сопромат. Но применительно к занимательному материаловедению нас интересуют в основном два из них:
прочность — способность конструкции выдерживать заданную нагрузку, не разрушаясь;
жесткость — способность тела или конструкции сопротивляться образованию деформации.
Если перевести на человеческий язык, то прочность говорит о том, насколько легко предмет сломать. А жесткость — насколько просто его погнуть таким образом, чтобы после этого он разогнулся обратно. Характеристики эти друг от друга не зависят: при одинаковой прочности материалы с легкостью могут иметь разную жесткость.
Еще есть твердость — она характеризует то, насколько легко поцарапать поверхность материала. Опять-таки ни с прочностью, ни с жесткостью напрямую она не связана.
Теперь от синтетики пора перейти к металлам. Для начала к магнию — вернее магниевому сплаву. Вообще говоря, этих сплавов существует целое семейство, и в зависимости от состава свойства сплава сильно меняются. Но конкретно в ноутбуках, как минимум в подавляющем большинстве случаев, используется пригодный для литья под высоким давлением сплав AZ91.
Обе половинки корпуса Acer TravelMate 8481 выполнены из магниевого сплава. Конструкция получилась настолько жесткой, что этим ноутбуком хочется срочно забить гвоздь-другой. Крышка в этой модели — из углеволокна
Собственно, в этом (помимо низкой плотности и высокой прочности) и заключается основная прелесть магниевого сплава — из него удобно отливать детали сложной формы. В этом отношении магниевый сплав несколько уступает популярным пластикам, но лишь самую малость: форма получается немного грубее, детали приходится дорабатывать. Но в целом это удачный материал для создания компактных устройств. За это его любят в том числе производители серьезных фотоаппаратов — у них потребность в сложных формах еще выше, чем у ноутбучников.
Корпус полнокадровой зеркалки Sony Alpha A99 изготовлен из магниевого сплава
А вот с чем у магниевого сплава откровенные нелады — это с презентабельным внешним видом, твердостью и стойкостью к коррозии. Детали из магниевого сплава в обязательном порядке надо анодировать и красить внешнюю поверхность, поскольку и сам металл, и образующаяся на его поверхности в процессе анодирования пленка чрезвычайно легко царапаются. После всей необходимой обработки деталь из магниевого сплава внешне становится практически неотличимой от пластиковой. Что, впрочем, совершенно не умаляет практических достоинств магниевого сплава. В целом на лицо этот материал не слишком прекрасен, но в душе — очень добрый.
В классических Lenovo ThinkPad внешние корпусные панели пластиковые. Но внутри скрыта прочная рама из магниевого сплава. Идея та же, что и с рамными внедорожниками, — пластиковый обвес смягчает удар и его не жалко повредить
Поскольку в случае магниевого сплава краска служит не только декоративным покрытием, но и защитным, магниевые детали всегда красят очень тщательно, солидным слоем стойкой к повреждению краски. В случае пластика повреждение покрытия грозит только потерей товарного вида. Так что красят более тонким слоем и менее серьезной краской — во многих случаях она быстро стирается, обнажая Красоту.
Переходим к следующему металлу — алюминию. А вернее, сплавам на его основе, поскольку рассматривать применение этого металла в чистом или практически чистом виде — это даже не смешно, просто вспомните советские вилки. Сплавов этих существует великое множество и по своим свойствам они различаются не просто сильно, а прямо-таки кардинально.
Apple MacBook Air : и корпус и крышка выточены из цельного бруска алюминия. Адски дорогой подход, зато весь металл — на виду
Господь ведает, какой из них использует в своих устройствах Apple, так что в качестве примера алюминиевого ноутбука рассмотрим вовсе не макбуки, а Samsung Series 9 образца 2012 года. Эти ребята, по крайней мере, честно маркируют корпусные детали, так что можно с уверенностью сказать, из чего именно они изготовили (вроде бы все еще) самый тонкий ноутбук в мире.
Самый тонкий ноутбук в мире Samsung 900X3C построен по тому же принципу, что и MacBook Air
А использовали они сплав AL6061, который принадлежит к числу алюминиевых сплавов с весьма хорошими характеристиками. Хотя он и не является чем-то из ряда вон выходящим. Скажем, из него делают сравнительно продвинутые велосипедные рамы (а именно из него их делают потому, что существующие более суровые сплавы алюминия не дружат со сваркой), также его используют при производстве автомобилей и постройке яхт.
Корпус Samsung 900X3C полностью выполнен из сплава AL6061
Сплав этот непригоден для литья, в чем, собственно, и заключается его главный недостаток, серьезно ограничивающий популярность в рассматриваемой нами сфере. Для AL6061 (а также других достойных внимания сплавов алюминия) есть два доступных способа получения готовой детали: штамповка и фрезерование. Первый вариант накладывает серьезные ограничения на форму детали. В общем случае таким образом можно получить лишь плоскую деталь, которую придется крепить к более сложно устроенной основе.
ASUS Zenbook Prime — тот же способ обработки алюминия, но с дополнительной декоративной составляющей: на крышке выточено множество концентрических окружностей, которые играют на свету
Фрезерование имеет некоторые ограничения по сравнению с литьем, но все же дает достаточно широкий простор для конструкторов. Так что при правильном проектировании выточенная из алюминиевого сплава деталь вполне заменяет отлитую из пластика или магниевого сплава. Однако у этого метода есть существенный недостаток: он чрезвычайно дорог по сравнению со всеми остальными способами производства.
Примерно так выглядит процесс фрезерования — кадр из видеоролика компании Apple, посвященного производству unibody-корпусов
Кстати о ценах. Все три популярных в ноутбукостроении материала — магниевый сплав, алюминиевый сплав и пластик ABS+PC — стоят примерно одинаково. Цена составляет около $3 000 за тонну. Если говорить о чистом поликарбонате, то он примерно на $1 000 дороже. Использование версий пластика, армированных стекло- или углеволокном, само собой, обходится еще дороже.
В чем же дело, почему в большинстве случаев производители все равно предпочитают использовать синтетику? Все дело в цене обработки. Скажем, если исходить из приведенных выше цен и того факта, что на корпус ноутбука уходит порядка одного-двух килограмм исходного материала, то несложно посчитать, что расходы составляют в среднем около $5 на одно устройство (в случае смартфона это и вовсе смешные десятки центов).
Однако стоимость работы при производстве корпуса ноутбука, выточенного из алюминия с последующим анодированием, примерно на $100 выше, чем корпуса, отлитого из магниевого сплава и окрашенного. Из пластика, само собой, получается еще дешевле, чем из магния, — как уже было сказано выше, он вообще не требует обязательной обработки после литья. Это очень весомые деньги даже для продуктов премиум-класса, а уж в бюджетном сегменте такие траты просто недопустимы.
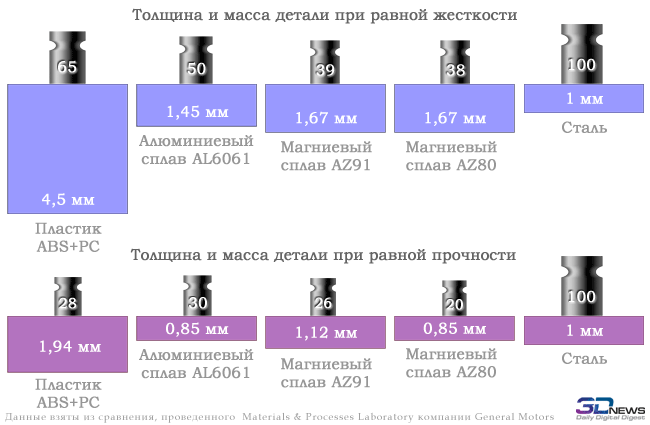
Стандартная смесь ABS+PC, как несложно понять из приведенной иллюстрации, обладает приличной прочностью, но недостаточной жесткостью. Чтобы корпусные детали не получались слишком гибкими, приходится делать их толстыми — в разы толще стальных, магниевых или алюминиевых. И по массе получается проигрыш по сравнению со всеми рассматриваемыми альтернативами, кроме стали.
Детали из магниевого сплава AZ91 в 2,5 раза легче стали при одинаковой жесткости и вчетверо легче — при равной прочности. Однако толщина деталей при этом должна быть сравнительно большой — особенно если требуется обеспечить высокую жесткость.
Алюминиевые детали можно делать несколько более тонкими, чем магниевые. Но в плане массы этот материал получается немного менее интересным, чем магниевый сплав. Кроме того, не следует забывать, что в рассматриваемом примере фигурирует весьма удачный по характеристикам сплав AL6061, между тем, в ноутбуках мы встречали и менее подходящие сплавы.
Так устроена крышка Samsung Series 5: штампованный алюминиевый лист плюс отлитая из пластика рамка со всеми необходимыми мелкими элементами
Существуют магниевые сплавы и с более брутальными характеристиками. Скажем, AZ80: он непригоден для литья, так что обрабатывать его пришлось бы примерно так же, как алюминий, — штамповкой одних деталей и фрезерованием других. С другой стороны, этот сплав при некоторых жертвах в жесткости позволил бы обеспечить значительное снижение массы по сравнению с алюминием и привычным AZ91. Возможно, мы еще встретимся с ним в каком-нибудь особенно воздушном ноутбуке.
Пластиково-металлический сэндвич в ноутбуке Acer Ethos 8951G. В данном случае металл толще пластика, но чаще бывает наоборот
Помимо чисто металлических и чисто пластиковых корпусов, существует еще и в некотором роде промежуточный вариант. Это то, что наиболее аккуратные в формулировках производители обычно называют «металлической отделкой». В этом варианте на основу — толстую пластиковую деталь — наклеивают тонкий лист металла. Такой подход позволяет отчасти компенсировать недостаточную жесткость «голого» пластика, но все равно проигрывает по характеристикам нормальным металлическим деталям. По большому счету, такой «бутерброд с жестью» предназначен только для того, чтобы радовать глаз.
В MSI X460 под жестянкой даже нет пластика — из-за этого левая часть области palm rest сильно нагревается расположенным под ней графическим адаптером
Суммируем все вышесказанное. В случае крупного настольного ноутбука рекомендуем не обращать слишком уж много внимания на то, из чего он сделан. Практической разницы все равно не будет — главное, чтобы пристойно выглядел и не слишком дорого стоил. Доплачивать за отделку особо ценными породами жести, вообще говоря, не имеет особого смысла — разве что доплата невелика.
Если же говорить о компактных моделях с претензией на ультрамобильность, то тут ситуация диаметрально противоположная. Без использования продвинутых материалов невозможно добиться приемлемого соотношения невысокой массы и достаточной жесткости корпуса. А от жесткости напрямую зависят тактильные ощущения от устройства и некоторые особенности практического характера. Например, то, насколько прогибается клавиатура в процессе печати или фиксируется ли нормально крышка ноутбука в открытом состоянии.
Очень похожие ноутбуки из-за использования разных материалов могут получиться очень разными
Использование пластика здесь допустимо, по крайней мере, если речь идет о синтетике, усиленной стекло- или углеволокном, но только в недорогих моделях. Все-таки даже «волокнистый» пластик в большинстве случаев проигрывает металлу по характеристикам — такие ноутбуки получаются одновременно и тяжелее, и гибче.
Что касается выбора между корпусами, выточенными из алюминия и отлитыми из магниевого сплава, то первый вариант предпочтительнее в эстетическом плане, второй — значительно дешевле и при правильном подходе обеспечивает несколько меньшую массу ноутбука. Красиво vs. практично — вечное противостояние.